Technology development
The Tokyo Ink Group’s technology, which has developed around a variety of color materials, consists of the five fundamental technologies of pigment dispersion, material design and compounding, kneading, forming, and analytical and evaluation.
These fundamental technologies support our core technologies that have competitive superiority and enable us to develop colorants and functional products that meet demands in a wide variety of fields.
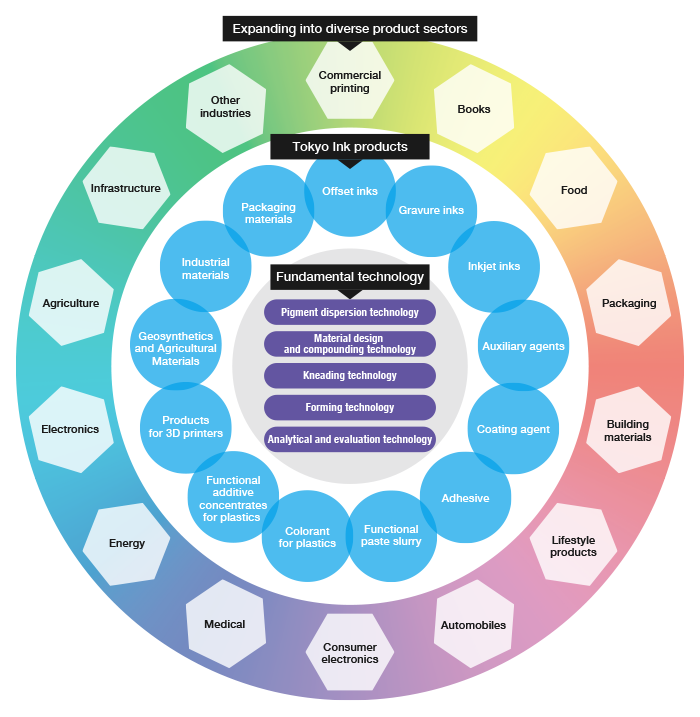
Fundamental Technology
-
Pigment dispersion technology
Many pigments are used as colorants, and when it comes to such use, the important thing is to uniformly disperse and stabilize the pigments in the base material in order to maintain the intended color in inks and resin molding materials. Therefore, technology is required to control the properties of the material by controlling miniaturization, particle size, wettability, and other such aspects, and to commercialize the material without pigment aggregation.
-
Material design and compounding technology
In order to increase product value, a wide range of suitable functional materials must be selected according to the environment and application of the final product, and a combination of processes and formulas must be used to maintain its stable performance, with an example being color mixing technology.
-
Kneading technology
Mixing and kneading technologies are important when it comes to ensuring pigment dispersion and material compounding technologies are effective. These technologies are indispensable for product design, as extensional flow and shear flow in action in the process of kneading require optimization of kneading equipment according to the material while appropriately controlling the operating conditions.
-
Forming technology
It is said that the quality of the mold determines the quality of the product. To design the product, we start with analyzing the shape and function required of the molded product, and then design the mold before fabricating it under optimal mold processing conditions. We have accumulated an abundance of design and molding technologies by undertaking molding in optimal molding conditions, evaluating the resulting molded products, and then feeding the results of evaluation back into product design.
-
Analytical and evaluation technology
Alongside production technology, technology to correctly evaluate the performance of products used in various fields is the foundation of manufacturing. We provide reliable products thanks to an evaluation technology based on a wide variety of analysis devices and analysis know-how.
Analytical Equipment
In the process of developing various products, the ability to accurately evaluate the performance requirements of customers and to feed them back to the design of formulations is essential when it comes to rapid product design.
In addition to providing reliable products designed by leveraging our deep analytical know-how, the Tokyo Ink Group proactively works to solve customers’ problems even after products have been delivered by analyzing issues that may subsequently arise.
In addition, we have registered Tokyo Printing Ink as a Working Environment Measurement Agency that can perform the working environment measurement by our own experts (Saitama, No. 11-45). This is to conduct measurement work related to organic solvents, mineral dust, specified chemical substances, and metals in compliance with laws and regulations (analysis in compliance with WEEE and RoHS regulations for products, etc.).
-
Structural analysis
- Laser Raman microscope
- Infrared spectrophotometer (FT-IR)
- Ultraviolet/visible spectrophotometer (UV-Vis)
- Gas chromatograph-mass spectrometer (GC-MS)
- Liquid chromatograph-mass spectrometry (LC-MS)
-
Chromatographic analysis
- Gas chromatograph (GC)
- High performance liquid chromatograph (HPLC)
-
Crystal structure analysis
- X-ray diffraction (XRD)
-
Thermal analysis
- Differential scanning calorimeter (DSC)
- Thermogravimetric analyzer (TGA)
-
Morphological observation and elemental analysis
- Field emission scanning electron microscope (FE-SEM)
- Wavelength dispersive X-ray fluorescence analyzer (WDX)
- Energy dispersive X-ray fluorescence analyzer (EDX)
- Inductively coupled plasma optical emission spectrometer (ICP-OES)
-
Molecular weight distribution measurement
- Gel permeation chromatography (GPC)
-
Physical property and other tests
- Full-automatic tensile tester
- Universal testing machine (UTM)
- Izod impact strength tester
- Laser diffraction Scattered particle size analyzer (LD)
- Karl Fischer moisture analyzer
-
Analysis pretreatment
- Ion milling device (IM)
- Osmium coater
- Microwave sample decomposition device (MW)
Technical Organization
There are two departments under our Production & Technical Division: Production & Technical HQ1, Production & Technical HQ2, and this provides us with a structure that enables efficient work encompassing everything from the systematic organization of elemental technologies to product development.
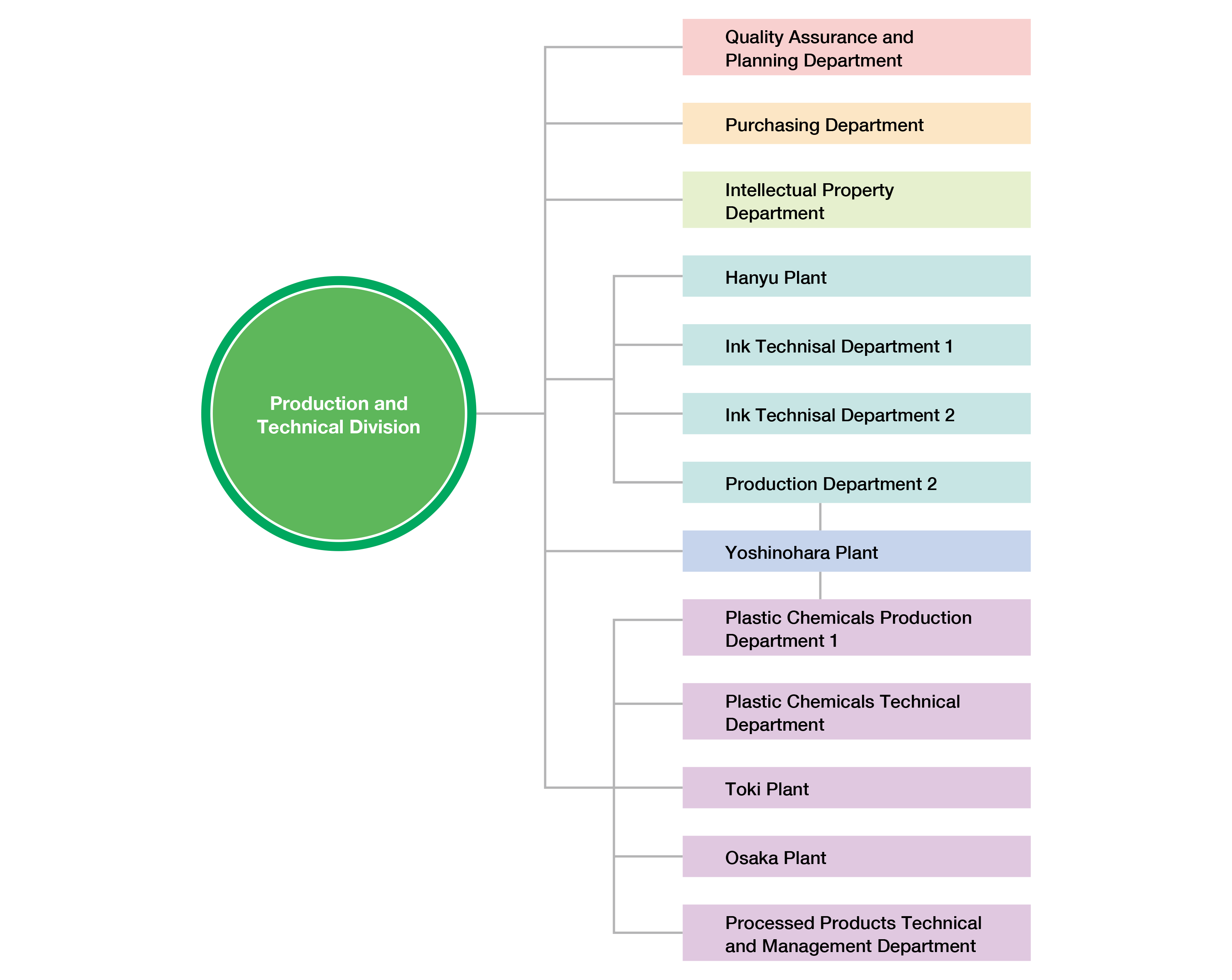